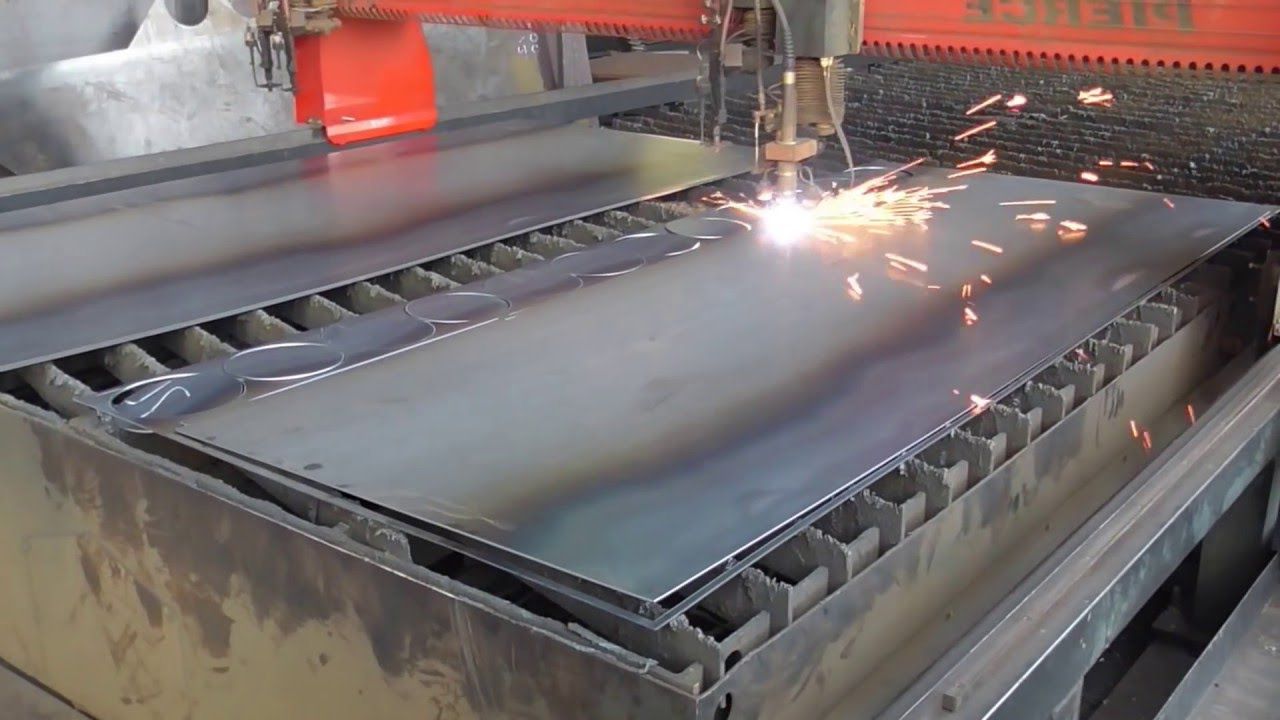
Plasma cutting uses an accelerated jet of hot plasma to cut through electrically conducting materials. Other conductive metals may also be cut with a plasma torch, however the most common materials to be cut with one are steel, stainless steel, aluminium, brass, and copper. In fabrication shops, vehicle repair and restoration businesses, commercial building projects, and salvage and scrapping businesses, plasma cutting is frequently employed. Plasma cutting is used widely, from large-scale industrial CNC applications to tiny hobbyist shops, thanks to the high speed and precision cuts mixed with the inexpensive cost.
Creating an electrical channel of superheated, electrically ionised gas, or plasma, from the plasma cutter itself, through the workpiece to be cut, so completing an electric circuit back, is the fundamental step in the plasma cutting process.Plasma cutting works well to cut both thin and thick materials. Stronger computer-controlled torches can cut steel up to 150 mm (6 in) thick, while hand-held torches can typically only cut steel plates up to 38 mm (1.5 in) thick. Plasma cutters are highly helpful for cutting sheet metal in curved or inclined shapes because they provide a very hot and localised “cone” to cut with.